GRENDEHL
GyRation ENabled Devices for
Extreme Hypervelocity Launches
FEATURES
- GRENDEHL – works by mechanical acceleration of payloads irrespective of mass
- Physics / engineering well understood
- Stealth signatures – no EMP, no propellant gas blast, limited to supersonic shocks –
weak N-waves & high-speed machinery acoustics - Low angular dispersion of launched projectiles
- No excessive barrel heating due to hot propellant gases or Ohmic heating
- Efficiency ∼50%, and better (half of energy or more goes into projectile)
- Pulse power demands relaxed by length of acceleration distances
- High launch rates – proportional to gyration frequencies (typically 30 – 90 gps, limited only by prime power)
- Safe – no explosives or propellants, no high currents/voltages involved in acceleration process
- Scalable from validated designs to high payload masses / velocities
- No special materials required in manufacturing
- Potential utility for routine delivery of matériel, fuels, structural materials to Low Earth Orbit (LEO)
and above with Earth surface launches (“Space Train”) - Routine mining ore transfer to Earth from moon-based accelerator using free-return orbits (“Moon Train”)
- Asteroid deflection using Moon facility to launch multi-ton impactors at tens of kilometers per second
- Routine supply train to Mars (“Mars Train”)
HISTORY OF EVOLUTION OF PROJECTILE ACCELERATION
Linear Acceleration
Centrifugal Acceleration
material strengths – fundamental barrier to centrifugal hypervelocity launches
- Swing arm – length L, density ρ, Young’s Modulus Y, yield stress σy
- Root radius (swing arm axle attachment): y(L)
- Root must be thick enough to support g-loaded (ng) projectile and swing arm
- Support must be provided throughout acceleration process → static yield stress governs structural integrity
- Plot of swing-arm mass (yellow) and swing-arm length (green – for selected g-loadings) as functions of launch velocity
- Assigned projectile mass: 100 kg. Results scalable to other payload masses
- Material stress everywhere in swing arm set to yield stress (no safety margin) (σy = 240 MPa for titanium)
- Note: extreme swing-arm mass requirements for launch speeds greater than about 1km/s rule out centrifuge launchers for suborbital and above applications
BREAKTHRU ACCELERATOR TECHNOLOGY → GRENDEHL
- Abandons swing-arm design
- Provides projectile inertial acceleration field by means of gyrating – not rotating raceway
- Projectile rides on gas bearing to achieve extreme efficiencies
- Projectile reaching launch velocity resides at any point of raceway for only extremely short times
→ dynamic stress hardening ensures raceway viability - Experimental results and rigorous modeling indicate improving gas bearing efficiency with increasing projectile mass and launch velocity
→ projectiles from tens of kilograms to tens of metric tons and launch speeds in tens of kilometers per second are feasible
Source of inspiration
Swirling the liquid and ice contents in a tumbler by moving it in a circle without rotation – fixed orientation (tumbler doesn’t slip in the hand).
Phase-locked spiral acceleration
- Vlaunch ≈ (outer radius/ gyration radius) × gyration velocity
- gyration velocity = 2π × gyration radius × gyration rate
- gyration period = 1/ gyration rate
- launch period = gyration period × number of turns
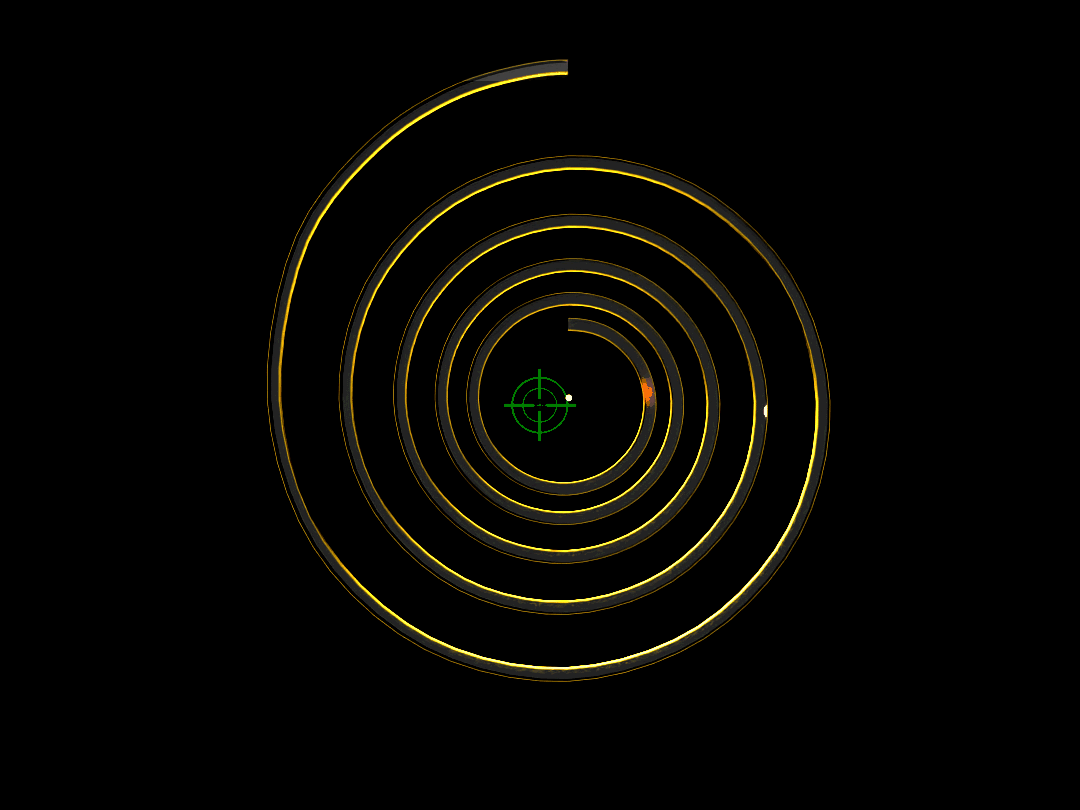
Animation: 1/30 real-time gyration rate
- Outer radius = 19.1 m
- Gyration radius = 1.59 m
- Number of turns = 5
- Gyration rate = 30 gps
- Gyration period = 33 ms
- Gyration velocity = 300 m/s
- Vlaunch = 3.6 km/s
- Time to launch (launch period) = 165 ms
- Note: both the gyration rate & g-loading can be decreased by scaling up the outer & gyration radii while holding Vlaunch & vgyration fixed
PROOF OF PRINCIPLE
PERFORMANCE
PARAMETERS | PROOF OF PRINCIPLE | BMG-50 |
---|---|---|
MASS | 228g (3519gr) | 45g (694gr) |
RADIUS (OUTER) | 0.5 m | |
RADIUS (INNER) | 7.6 cm | |
GYRATION FREQUENCY | 42 gps | |
V-LAUNCH | 800 m/s | 908 m/s |